Pigging System Application: Unlocking Efficiency Across Modern Industries
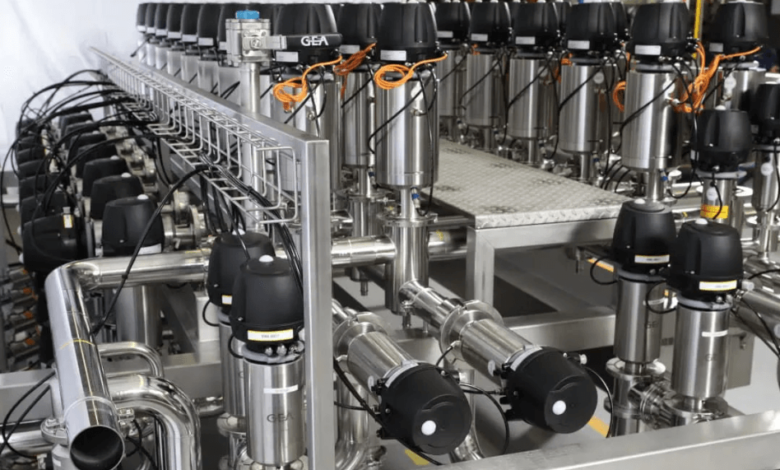
In today’s fast-paced industrial world, efficiency, sustainability, and cost-effectiveness are critical to maintaining competitiveness. Whether you’re in the food industry, pharmaceuticals, paints, personal care, or chemicals, product recovery and line cleaning are daily challenges. This is where the pigging system application proves to be an innovative and indispensable solution.
From reducing product loss to minimizing contamination, pigging systems have become essential to modern liquid processing operations. In this article, we’ll explore the principles, components, and most importantly, the broad pigging system application across various industries.
What is a Pigging System?
A pigging system is a mechanism that uses a specially designed object—called a pig—to travel through pipelines. The pig scrapes residual product from the inner pipe walls, pushing it toward its destination, and leaves the pipeline clean and ready for the next process.
These systems are widely implemented to:
- Recover high-value product left in pipelines
- Minimize waste
- Reduce cleaning time and water/solvent usage
- Prevent cross-contamination between different batches
The pigging system application is particularly advantageous in industries where the cost of lost product is high or where cleanliness and hygiene are mandatory.
See also: Discover the Art of Bespoke Living with Kitchen Installers and Fitted Kitchens
How Does a Pigging System Work?
While there are several variations of pigging systems, the fundamental operation is consistent. The process includes the following stages:
- Pig Launching: A pig is inserted into the pipe via a launcher station.
- Product Transfer Completion: Once the product has been moved, a pig is pushed through the pipeline using a medium like compressed air or nitrogen.
- Product Recovery: The pig pushes the remaining product forward, which is then collected and used.
- Pig Receiving: The pig is captured at the end of the line in a receiver or returned to the start point in automated systems.
The process is fast, efficient, and often fully automated.
Pigging System Application Across Industries
The pigging system application spans a diverse range of industries. Let’s look at the most common sectors and how they benefit:
1. Food and Beverage Industry
In food processing plants, pipelines carry high-viscosity products such as sauces, syrups, jams, and dairy products. Leaving even a small residue inside the line leads to significant product loss.
Applications:
- Transferring tomato paste, mayonnaise, or yogurt with minimal waste
- Enabling quick switchovers between flavors or ingredients
- Maintaining hygiene standards and reducing contamination risk
Benefits:
- Saves valuable ingredients
- Reduces cleaning time
- Decreases water and CIP (Clean-In-Place) usage
2. Cosmetics and Personal Care
Products like lotions, shampoos, gels, and creams are expensive to manufacture and often have short shelf lives. Pigging is vital for transferring these liquids while preserving their quality.
Applications:
- Moving body wash from blending tanks to filling machines
- Switching between product lines (e.g., from hair conditioner to facial cleanser)
- Keeping fragrance or color carryover at zero
Benefits:
- Maximized product yield
- Reduced waste
- Cleaner transitions between batches
3. Pharmaceutical Industry
In pharma, the importance of cleanliness, compliance, and zero cross-contamination cannot be overstated. Pigging provides a hygienic and controlled method for product recovery and transfer.
Applications:
- Recovering syrups, oral suspensions, or injectable solutions
- Cleaning lines with minimal solvent
- Improving batch integrity and reducing contamination risks
Benefits:
- Meets stringent FDA and GMP requirements
- Ensures product purity
- Increases productivity with faster cleaning cycles
4. Paints and Coatings
Paint manufacturers often deal with color-sensitive or solvent-based products. Every drop of residue left behind can mean contamination or costly disposal.
Applications:
- Transferring colored paints, primers, or coatings
- Cleaning lines during color changes
- Handling hazardous materials with minimal manual intervention
Benefits:
- Drastic reduction in solvent use
- Recovery of expensive pigment-based products
- Improved worker safety
5. Chemical and Industrial Liquids
Chemical plants use pigging to move high-value, viscous, or hazardous liquids. This sector sees great return on investment due to the sheer volume of product saved.
Applications:
- Moving adhesives, resins, lubricants, or solvents
- Managing corrosive fluids with minimal exposure
- Reducing flushing chemicals and waste handling
Benefits:
- Significant cost savings
- Safer operations
- Lower environmental footprint
Types of Pigging Systems
Depending on the industry and application, the pigging system can be customized in various ways:
- Single Pig Systems: Basic setup for cleaning and product recovery
- Double Pig Systems: Two pigs isolate the product slug for ultra-clean transitions
- Automated Systems: Fully integrated into SCADA or PLC for hands-free operation
- Hygienic/Sanitary Systems: Designed for food and pharma with strict hygiene controls
Each configuration enhances a specific pigging system application based on production needs.
Key Components of a Pigging System
Every pigging system typically includes:
- Pigs: Made of elastomer or silicone, designed to match pipe diameter
- Pig Launchers and Receivers: Entry and exit points for pigs
- Piggable Valves: Allow pigs to pass without obstruction
- Control System: PLC or manual control panel to initiate sequences
- Propellant Supply: Compressed air, CO₂, or nitrogen to move the pig
Proper design and component selection are crucial for efficient pigging operations.
Pigging System ROI
The return on investment (ROI) of pigging systems is often realized within 6 to 12 months, especially in high-volume operations. The key ROI drivers include:
- Reduced raw material waste
- Lower cleaning and water costs
- Faster changeover times
- Less downtime and labor usage
Businesses also benefit from improved sustainability, which supports regulatory compliance and corporate social responsibility.
Future Trends in Pigging System Application
As technology evolves, so does the potential of pigging systems. Expect to see:
- Smart Pigging: Integration with IoT for predictive maintenance
- Automated Product Changeovers: Linked with ERP systems
- Eco-Friendly Materials: For pig construction and cleaning media
- Industry 4.0 Compatibility: Fully digitized pigging process control
These advancements ensure pigging remains a future-ready solution for fluid processing industries.
Conclusion
The versatility and efficiency of pigging system application make it an essential tool in modern manufacturing environments. From food to pharmaceuticals and from cosmetics to chemicals, the ability to recover product, clean pipelines, and reduce waste is no longer optional—it’s a necessity.
As industries continue to push for zero waste, better quality, and cleaner production processes, pigging systems offer a proven solution. By understanding and applying this technology across different sectors, businesses can stay ahead of their competition while contributing to a more sustainable and efficient future.
.